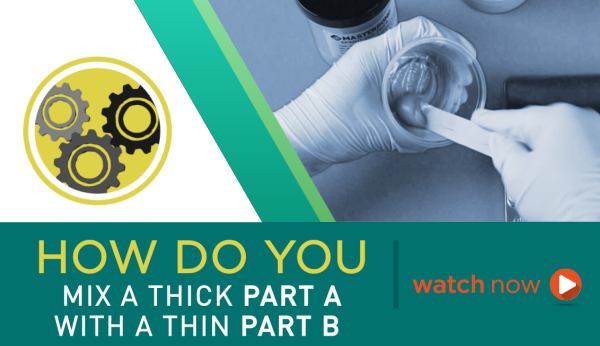 |
Proper and precise measuring and mixing are key steps to ensure that your adhesive will perform in the manner that you are expecting. This step can be more challenging when dealing with formulations that have widely varied viscosities between Parts A and B. Our technical experts have a demo that offers some tips and techniques to correctly mix your two component system.
|
Here are some two component epoxy and silicone systems with a significant disparity in viscosity which can use the same mixing technique:
EP42HT-3AO: High Glass Transition Temperature
For more information, request a technical data sheet on EP42HT-3AO
EP30LTE-LO: NASA Low Outgassing Two Component Epoxy
For more information, request a technical data sheet on EP30LTE-LO
EP29LPSPAO-1 Black: Forgiving 100 to 65 Mix Ratio by Weight
For more information, request a technical data sheet on EP29LPSPAO-1 Black
Supreme 45HTQ: Quartz Filled, Heat Resistant Epoxy
For more information, request a technical data sheet on Supreme 45HTQ
MasterSil 151TC: Highly Flexible Addition Cured Silicone
For more information, request a technical data sheet on MasterSil 151TC
EP21TDC-2LO: Flexible, Thermally Conductive Epoxy
Note that this compound has a 1 to 3 mix ratio by weight or volume. Part A has a thickness of 35,000-85,000 cps while Part B has a heavy viscosity of 300,000-800,000 cps. The same mixing technique can be applied, but the process should start by adding a thicker B part first.
For more information, request a technical data sheet on EP21TDC-2LO
|
|
|
Copyright 2018 by Master Bond Inc. All Rights Reserved. This content may not be reproduced in any way without the prior written permission of Master Bond Inc.
|
|