Overview of UV11-3
Master Bond UV11-3 is a hard, super-abrasion-resistant coating system for plastic substrates. It can be cured readily by ultraviolet (UV) exposure or electron-beam radiation either in the air or under inert atmospheres such as nitrogen. When cured, Master Bond UV11-3 features optical clarity, as well as high hardness and abrasion resistance. It is especially suitable for applications where optical transparency is required, such as the creation of photo-cured waveguides for lithium niobate chips.
Application
Lithium niobate (LN) is used in advanced photonics due to its high optical non-linearity and optical transparency. Researchers at City University of Hong Kong have developed a self-written waveguide (SWW) to reduce the coupling losses that occur between optical fibers and integrated LN chips. This waveguide was created using photo-curable Master Bond UV11-3 by modifying its structure so that it could be cured using a 532 nm green laser, as shown in Figure 1.
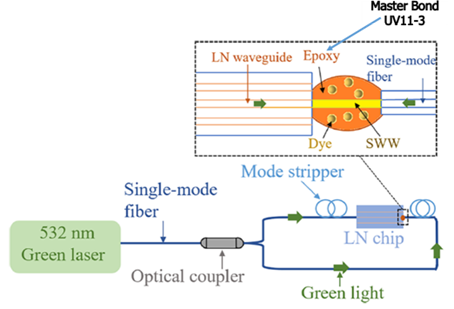
Figure 1. Schematic diagram of the SWW formation process between the LN waveguide and the SMF under double-side irradiation. (Modified from He et al., 2023.)
Key Parameters and Requirements
Because LN is optically transparent, it is suitable for use with fabrication techniques such as visible-light curing, which typically cannot be used with traditional silicon photonics. When un-modified, UV11-3 can only be cured using UV light or electron-beam irradiation. Therefore, the authors doped UV11-3 with Rhodamine 6G dye, which allowed it to be cured with a 532 nm green laser (1.36 mW) within 15 minutes when using a dye concentration of 0.5 wt%.
Results
Figure 2. (a) Microscopic image of the SWW formed between the SMF and the LN waveguide; zoom-in (b) optical microscopic, and (c) SEM images of the SWW connected to the LN waveguide. (Taken from He et al., 2023.)
The SWW provided an optical link that confined and guided the light, ensuring that it was transmitted from the fiber to the LN waveguide. The authors optimized the green light power and dye concentration to reduce coupling losses between the fiber and LN chip and showed that double-sided irradiation resulted in a greater decrease in coupling losses. In this way, the SWW was grown from both the LN waveguide and SMF ends during the photo-curing of UV11-3 (Figure 2).
As noted by the authors, Master Bond UV11-3 was selected for forming the SWW because of its optical transparency, broad service temperature range, and low viscosity. Because of these properties, UV11-3 played a key role in reducing coupling losses when cured into a self-guided waveguide.
Sources
Liangjun He, Hanke Feng, Cheng Wang, and Hau Ping Chan, "Cost-effective fiber-to-lithium niobate chip coupling using a double-side irradiation self-written waveguide," Opt. Lett. 48, 283-286 (2023)