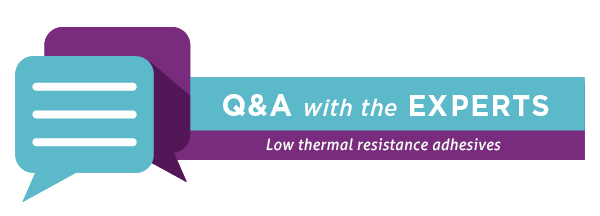
Join Venkat Nandivada, Manager of Technical Support at Master Bond, as he answers questions about adhesives with low thermal resistance.
Q: Why is there a need for low thermal resistance adhesives?
A: As the electronic industry continues to yield faster, high-density devices, materials capable of coping with increasing heat loads are essential. The ability of thermally conductive adhesives to help dissipate heat has motivated their use as the preferred fastening approach in applications requiring careful thermal management. Moreover, adhesives with very low thermal resistance characteristics aid in extending electronic device performance, service life, reliability and integrity.
Q:What are some of the products that Master Bond has developed to address the needs of the industry?
A: Supreme 18TC is a one component epoxy with very low thermal resistance and high thermal conductivity that is also NASA low outgassing approved. Supreme 18TC can be applied in bond lines as thin as 10-15 microns, which leads to higher heat dissipation. It offers an exceptionally low thermal resistance of around 5-7 x 10-6 K•m2/W. The bottom line: Supreme 18TC has very low thermal resistance, since it is able to cure effectively in very thin layers. Another way of looking at this is to say that the lower the thermal resistance, the better the heat transfer.
Another product is EP48TC. This two component adhesive features similar heat transfer capabilities as Supreme 18TC. It has an optimum cure schedule of overnight at room temperature, followed by 3-5 hours at 150-200°F. EP48TC also features minimal shrinkage upon curing, a low coefficient of thermal expansion, and a Shore D hardness of 85-95. Both products have excellent electrical insulation properties over a wide service temperature range.
One example of an electrically and thermally conductive epoxy is EP3HTSDA-2, which is a one component, silver filled system, that offers an exceptionally high thermal conductivity of 45-49 BTU•in/(ft2•hr•°F) [6.5-7 W/(m•K)].
Q: Why is a thin bond line desirable?
A: The thickness of the bond and nature of the surfaces meeting at the bond interface can work to impede heat transfer. Consequently, manufacturers look to join materials with the thinnest- possible bond lines. In fact, a thin bond line is preferred over a thick one, since it helps to reduce the thermal resistance and increase heat dissipation. The particle size of the thermally conductive filler in the adhesive can contribute to a trade-off between optimal bond strength and optimal heat transfer.
The bulk thermal conductivity specification addresses only part of the objective of internal heat transfer. In a typical product assembly, a more practical characteristic is the material’s thermal resistance. Thermal resistance describes the ease with which heat can transfer across the interface between the die (or component) surface and bonding material, across the bonding material, and finally across the interface between the bonding material and package (or heat sink).
Q: What are some of the devices where Master Bond thermally conductive adhesives are currently employed?
A: Some examples are: Microprocessor assembly, bonding and potting power supplies, rectifiers and voltage regulators, bonding flexible and rigid circuit boards, mounting heat sinks, encapsulation of transformers, sensors, and coils, power supply components, chip bonding, waveguide assemblies, sealing connectors and pins, and staking diodes and resistors.
Q: In what industries is there a demand for thermally conductive adhesives?
A: Besides their use in areas such as power electronics and solar energy, thermally conductive adhesives play a vital role in the rapid growth of the LED lighting industry. By using these adhesives, LED providers are able to deliver highly efficient LED lighting products. Furthermore, because these adhesives remain resistant to typical environmental stresses such as weathering and corrosion, these products can help deliver the extended operating life expected in the marketplace.
Master Bond thermally conductive products can be used in a variety of industries, including electronic, aerospace, medical, optical, cryogenic, OEM, and many other high technology industries where optimum thermal transfer properties are a necessity.
Meet Our Tech Expert: Venkat Nandivada
Venkat Nandivada is the Manager of Technical Support for Master Bond Inc., a custom formulated adhesives manufacturer. He analyzes application oriented issues and provides product solutions for companies in the aerospace, electronics, medical, optical and oil/chemical industries. He graduated from Carnegie Mellon University with a Masters Degree in Chemical Engineering.