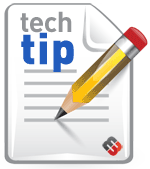
Crosslinking occurs when a thermosetting polymer such as an epoxy, cures via a chemical reaction either through the addition of heat, UV light exposure, or at room temperature itself. The origin of this crosslinking process occurs when linear polymer chains link to form a three dimensional network (See Figure 1)1. The resultant crosslinked polymer network is defined by the crosslink density, which is essentially the number of effective crosslinks per unit volume. Polymers with a high crosslink density typically cure fairly rigid, and offer good structural strength, while polymers with a low crosslink density, tend to be more flexible. This might be useful in applications requiring lower stress.
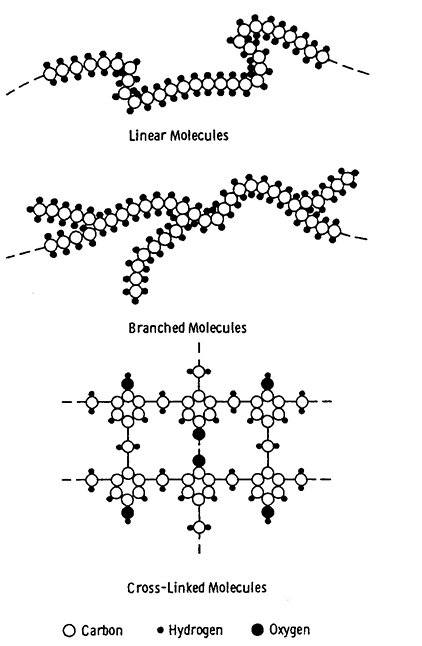
Crosslink density as it pertains especially to rigid curing epoxy systems is vital not only in providing a high glass transition temperature, but also in maximizing key physical strength properties such as tensile strength. Although the manufacturer’s curing recommendations are not set in stone, it is highly advisable to follow them as closely as possible for maximizing results. For any epoxy system, the crosslink density plays a vital role in achieving the right glass transition temperature. Not only is curing at the right temperature important, it is also critical to follow the right sequence in terms of temperatures. By doing so, the epoxy will achieve the most optimum result for the desired application and environment that it will be subject to. Curing at elevated temperatures will help achieve the highest crosslink density (highest glass transition temperature), and will also speed up the cure significantly. For example, if one were to cure a one component heat curing epoxy at 175° C for 1 hour, versus 125° C for 1.5 hours, the Tg and physical strength properties will most likely be higher with the higher temperature cure.
It also must be noted that there could be differences in application parameters such as substrates, geometries, configurations, temperature service conditions, chemical exposure, and mechanical stresses. Therefore, it is advisable to pay careful attention to the cure schedule as well as the cure temperature sequence to achieve optimal performance properties.
Source:
1Petrie, Edward. Handbook of Adhesives and Sealants. McGraw Hill.