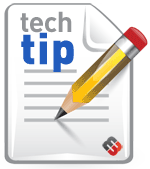
The adoption of medical grade plastics for single-use and multiple use devices/instrumentation continues to grow significantly. Design engineers are selecting biocompatible plastics to reduce weight/size, lower costs and improve performance. Commonly employed polymers include polyethylene, polypropylene, polyester, polycarbonate, polyethersulfone, polysulfone and polyetheretherketone. These plastic materials can be molded/extruded/cast/thermoformed in different shapes/sizes to meet tight tolerances. From valves, pumps, surgical instruments to prosthetics and imaging machines healthcare manufacturing companies rely on polymers to fulfill demanding requirements.
Master Bond offers a multitude of USP Class VI and ISO 10993-5 approved adhesive formulations for joining medical grade plastic substrates. These epoxies, silicones, cyanoacrylates and UV/LED curable adhesives are designed to replace mechanical fastening/solvent welding and bond well to similar/dissimilar surfaces. Products are application specific. Grades feature excellent tensile, compressive, impact and wear resistant properties. Flexible systems have high elongation, superior durability and outstanding peel strength. Compounds also offer thermal stability, are sterilization compatible, withstand hospital cleaners and have radiopacity. Optimizing the bond strength requires plasma or corona treatment, priming, chemical etching, surface roughening or flame treatment depending on the plastic being adhered.