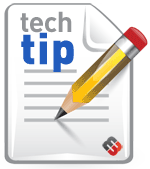
Select Master Bond epoxy adhesive formulations are engineered to prevent deformation/warpage, interface debonding, fatigue crack growth from residual stress caused by adhesive shrinkage. Volumetric change taking place during curing/crosslinking process can have a detrimental effect on bond integrity, durability, longevity, alignment and influence how the interface is formed. The greater the magnitude of cool down after cure, the greater the stresses, which will be reflected in significant out-of-plane deformation on warpage. Therefore the rate of cool down is critical for efficient performance/reliability of devices/structures under externally applied loads and thermal cycling.
Design engineers need to carefully evaluate the effect of bond line thickness, expansion/contraction coefficients of adhesive/adherend, operating temperature fluctuations, modulus of elasticity, glass transition temperature, part geometry, surface preparation to determine the suitability of different adhesives for structural bonding. Premature failure in adhesive bonds for large CTE mismatched surfaces can be induced by heat during curing or elevated temperature in service. Delamination/debonding from fatigue damage at the interface can be the result of temperature cycle aging. It is important to note that lower temperature curing conditions can reduce residual stresses and that allowing the epoxy to pre-gel prior to curing at a higher temperature (step curing) help achieve this objective.