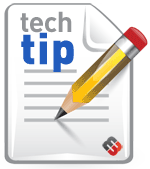
Epoxies are thermoset polymers with impressive physical strength, temperature, and chemical resistance among many other desirable properties. They have many functions not just limited to bonding, sealing, and coating, but also for casting applications. However, in casting applications, their exceptional adhesive properties to a wide variety of substrates can present problems with trying to remove the epoxy from the mold. There are a few techniques that can be used to overcome this problem.
Depending upon the application, the housing or shell of the casting is most commonly made from metals or plastic materials that epoxies normally will bond very well to. In order for the epoxy to be removed, a mold release agent must be first applied to the housing. There are many mold release agents commercially available for this kind of application. The choice of the release agent depends upon the precise nature of the substrate and the epoxy, the size of the casting, ease of application, health and safety considerations, as well as cost. Two of the more popular mold release agents are fluoropolymer based entities (such as PTFE) and polysiloxanes (silicones), although there are certainly a number of other types that are available as well. Mold release agents are typically applied by spraying on to the substrate / housing. An alternative approach is to have the mold itself made from silicone rubber or a fluoropolymer such as Teflon. Epoxies will not bond to these substrates, and they do not affect the curing of the epoxy either.
Ultimately, the objective is to have the mold be as unobtrusive to epoxy curing as possible, and that the epoxy casting be removable from the mold seamlessly.