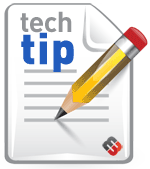
Addition curing systems are two part silicones which require the mixture of a silicone polymer with a catalyst to initiate the cure. These offer several advantages over one part systems, especially in production environments.
Since it is the catalyst and not moisture, as in the case of a condensation curing silicone, that causes the cure, they have no issue with section thickness. In fact, they can be used for applications such as potting, encapsulating and large castings. Two part systems do not release reaction by-products so they can cure in closed environments. Their cure can be greatly accelerated by heat curing. In a production environment, some systems can be given a fast, partial heat cure to facilitate a quick setup of the adhesive after which the work piece is allowed to finish curing at room temperature off the production line.
One major disadvantage of addition curing systems is that certain substances and substrates may inhibit their cure. One must be cognizant of materials in the application and cure area that can cause inhibition. Care must be taken to avoid contamination from other silicone RTVs that are cured with metallic salts, chlorinated rubber compounds, PVC plasticizers, amines, sulfur containing materials and butyl elastomers.
Master Bond offers several specialty addition curing silicones in its MasterSil product line.
MasterSil 155 is a graphite filled, electrically conductive silicone for electronic and electrical applications.
MasterSil 151 is a potting and encapsulation material especially well suited to opto-electronics. It is also available in a thermally conductive version called
MasterSil 151AO and in a medical grade version that passes USP Class VI testing called
MasterSil 151Med.