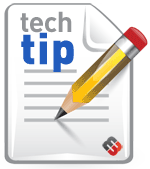
Superior tensile strength adhesives from Master Bond are employed in many critical bonding applications. One such application is the ASTM C633 adhesion testing of flame spray coatings. This test determines the adhesion or cohesion strength of thermal spray coatings, and it requires an adhesive with exceptionally high tensile strength to be able to quantify the strength of the coatings. Master Bond’s EP15 series has been designed exactly for this purpose.
The key point to note is that there are a wide range of substrates being bonded in thermal spray tests. The nature of the substrates being bonded will dictate which version of EP15 should be used. For example, EP15, which has a moderate, flowable viscosity, is preferable when dealing with porous materials, such as ceramic substrates. The non-drip paste version, called EP15ND-2 on the other hand, is preferable for non-porous materials, such as metallic substrates.
Sample demonstrating difference in viscosity of epoxy system EP15 versus its alternative non-drip version EP15ND-2.
If the substrates being used are semi-porous, or if there is a combination of porous and non-porous materials, the best approach is to start testing with EP15, and add a small amount of fumed silica (thickening agent), if required, in order to achieve the right consistency. It is recommended to first add around 1.0% of the thickening agent by weight to EP15, and then perform experiments by slowly increasing the percentage of the thickening agent, in order to determine the optimal amount.
The thickening agent is typically a very fine powder, and preheating EP15 at temperatures such as 60°C will temporarily reduce its viscosity and make it easier to mix in the thickening agent. Mixers (such as a planetary mixer) can be used to mix in the thickening agent. However, it can also be done by hand using tongue depressors or similar tools. It is recommended to dispense some EP15 into a cup first, and then mix in the thickening agent slowly with a spatula or similar tool. If the eventual formulation is flowable enough, it can be put into a syringe for application. However, if it’s too thick, it may have to be applied by hand with a spatula. Regardless of the mixing and dispensing method used, proper PPE needs to be employed, including but not limited to gloves and safety goggles.
After proper measuring, a tongue depressor is used to carefully mix in the thickening agent yielding a higher viscosity, non-drip paste.
Finally, it is also important to note that with any application, the product functionality is very technique dependent. Surface preparation and cure schedules can play a crucial role in the product functionality.
Adhesives for ASTM C633 Tensile Testing
![]() |
EP15 No mix compound has exceptional tensile strength properties. Superior dimensional stability. Used for testing the adhesion and/or cohesive strength of flame sprayed coating per ASTM C633. Low shrinkage upon cure. Viscosity 40,000-65,000 cps. Serviceable from -60°F to +250°F. |
![]() |
EP15ND-2 No mix compound has exceptional tensile strength properties. Superior dimensional stability. Used for testing the adhesion and/or cohesive strength of flame sprayed coating per ASTM C633. Low shrinkage upon cure. Viscosity 40,000-65,000 cps. Serviceable from -60°F to +250°F. |