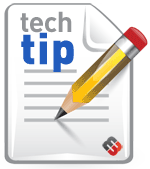
When designing adhesive bonding applications, optimizing joint design is an important consideration. Adhesive joints are not geometrically limited the way their mechanical fastener counterparts are. This leaves designers free to focus on the various mechanical and chemical stresses a specific joint is expected to withstand at its anticipated service temperature range. During the design phase, particular attention must be paid to the potential effects of mechanical shock and vibration, especially in dynamic bonding applications. Furthermore, assembly, manufacturing methodology, and cost factors must all be taken into account when proposing a joint design.
An understanding of the various possible joint designs for application is an essential step to finding the optimum bonding solution. Typical joint design and stress development data offers designers a number of choices. The following shows the most widely employed types of joint designs in use today:
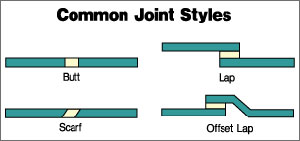
The butt joint is the simplest design. It is simply bonding two parts end to end. Generally, butt joints are not recommended for applications where available surface area is less than ½ to 1 inch, such as thin films, sheets and fibers. Bonding strengths for properly designed butt joints can vary from 800 psi in excess of 3,000 psi.
Scarf joints are similar, but have the joints leveled at matching angles to enhance the surface area available as well as increase the shear resistance. Shear stresses set in a plane with two substrates moving in opposite directions occur very often. Most structural adhesives can withstand 2,000-3,000 psi of shear stress at ambient temperatures.
In a lap joint, two substrates are joined by bonding together large surfaces of each piece. Bonding the same substrates by using the butt or scarf joints would result in less surface area being joined than a lap joint. However, while lap joints allow more bonding area, they can result in offset surfaces being susceptible to peel, which occurs when one of the substrates is deformed and pulled away from the bond line of the other substrate. Less commonly used, cleavage stresses develop when tensile forces are unevenly applied to one edge of a joint; forcing it to open. Both cleavage and peel failures decrease the effective surface area of the bond and can initiate “unzipping” between the substrates as pressure continues to be applied to the joint.
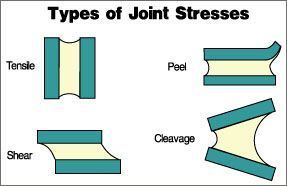
When subjected to tensile stress, the two substrates pull away from each other, perpendicular to their surfaces, while compressive stresses occur when the substrates are forced towards each other. Structural adhesives typically have tensile strengths from 8,000 psi to 12,000 psi and compressive strengths of 10,000 psi to more than 40,000 psi.
In closing, it would be remiss not to stress the impact and importance surface preparation has on bonding. Many adhesive designers fail to optimize their bond assemblies because they do not properly prepare the surfaces prior to adhesive application. Pretreatment methods generally consist of chemical etching or mechanical abrasion methods, employing grit blast media or aggressive solvents as well as special methods such as plasma or corona treatments. Proper surface pretreatment can greatly enhance the strength of a joint.
Master Bond’s experienced technical staff is available to help designers select an adhesive system, recommend surface pretreatment options, and suggest other ways to optimize the strength and durability of their designs.